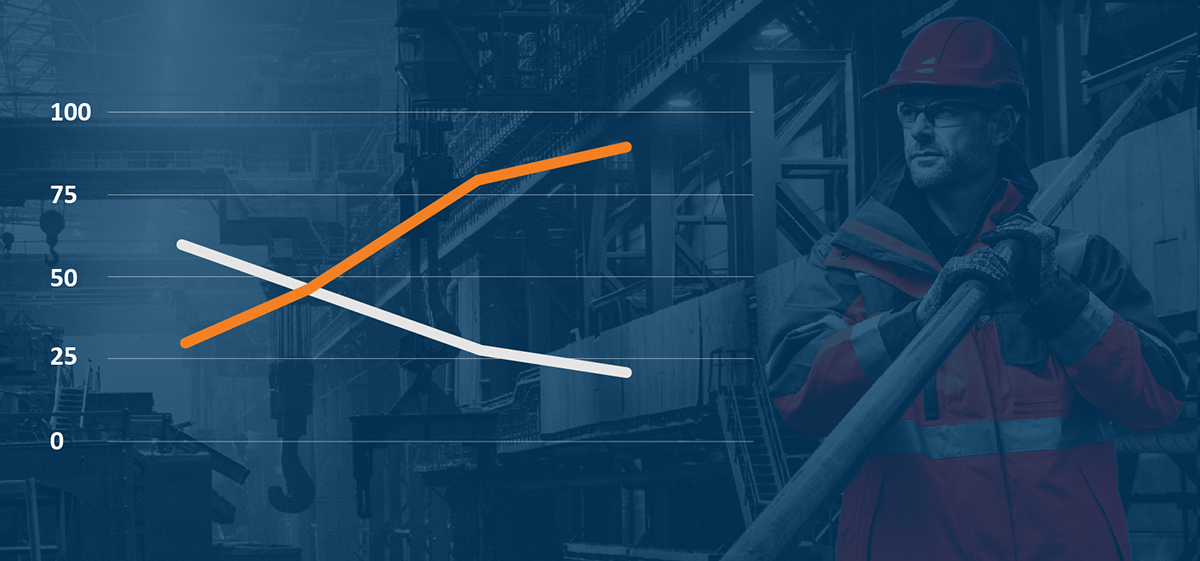
How to Maximise the Value of Safety Data in PPE Selection
Most organisations have access to a wealth of data about safety exposures, near misses, incidents, and accidents. However, this data only becomes Safety Intelligence – and can have a real impact on safety outcomes – when it is collated, analysed, and deployed in a coherent and consistent way.
Safety data is routinely used to improve an organisation’s understanding of their exposures. It informs the development of safety initiatives from toolbox talks, through behavioural safety processes, and all the way up to enterprise-wide safety culture and leadership programmes.
However, in our experience, it is all too infrequently used systematically as the basis of making truly informed decisions about providing best-in-class Personal Protective Equipment (PPE). Used intelligently, your safety data can help you understand not only what equipment to source, but also how to navigate the myriad cultural and behavioural challenges that impact wearer engagement and adoption.
Read on to learn about how to maximise the value of leading and lagging safety data, and the critical questions you should ask yourself before you place an order.
Utilising lagging indicators to inform your PPE choices
Lagging indicators like Total Recordable Incident Rates, Lost Time Injury Frequency Rates, and Medical Treatment Case Rates are often used to look back on injuries and incidents. However, this data can also be used to identify trends and areas where you may need to rethink your PPE – especially when combined with high-quality incident investigation reports.
Even the most basic analysis of your lagging indicators will give you a complete overview of incidents in a given period of time, including how many were hand injuries, how many were eye injuries, and so on. This data is invaluable in understanding where and how people are getting hurt – and more importantly how to prevent recurring incidents. It should periodically and systematically be fed back into your PPE procurement process and to your PPE suppliers for their analysis and professional recommendations.
Your incident investigation reports will also give you more detailed insights into the multiple root causes of a given incident. If you find too many of these investigations claim to result in a single root cause, such as “failure to wear correct PPE”, this should always be a red flag in your Safety Management System.
In practice, we all know that every incident is the result of a number of contributing factors and multiple root causes in the final common pathway to an accident – just one of which could be failure to wear the right PPE.
Techniques such as Tap Root® or The Five Whys can help you to uncover the downstream root causes, by identifying;
- Why wasn’t the right PPE available?
- Why wasn’t it used?
- Why is it not adopted and worn as a matter of habit?
- What makes workers feel it’s culturally acceptable to
not wear the right PPE and therefore put themselves at risk?
Used consistently, lagging indicators will show you where problems exist and where PPE needs your attention. All too often, incident investigation reports highlight “Failure to wear the right PPE” as the root cause – but multiple root cause analysis will help you understand the true nuances of failures in the safe and consistent adoption of Safe Working Practices and the wearing of the appropriate PPE.
Utilising leading indicators to inform your PPE choices
Leading indicators provide excellent opportunities to stay ahead of the exposures in your organisation and take meaningful pre-emptive action
before
anyone is hurt – or worse.
Near Miss and Hazard Reporting systems, employee surveys, management safety walkabouts, and Behavioural Safety processes all give excellent early warning of future accidents – if you take the time to listen to them. A systematic approach to mitigating risks, removing barriers to safe behaviour – and yes, providing the right PPE for the task that your employees will want to wear – is something that best-in-class PPE strategies and suppliers adopt as the norm.
In one real-life example, one of our newly-acquired customers had experienced an incident where an employee had their face burned by an escape of steam that partially blinded him in one eye. While this was the first recordable incident of its kind, the issue had been reported as a near-miss on several occasions and had been noted in a number of behavioural safety observations.
In this case, the answer was simple – the face mask supplied by the company's previous PPE provider left the face exposed if a wearer turned to either side. A change to the PPE specification and a switch to an improved face mask would have mitigated the exposure quickly, consistently and affordably. It was truly unfortunate that the company’s leading indicator and early-warning systems weren’t hard-wired into the PPE specification and procurement processes with their former supplier, as they could easily have prevented the accident and the associated personal hardship, compensation costs, and cultural impact.
Proactive and comprehensive leading indicators can involve huge amounts of data. With so many near misses and observations to record, it can be hard to spot the trends that matter most. In our opinion, it’s therefore critical that your PPE provider understands the issues and can help you turn your data into real safety intelligence.
How you can get more from your safety data
While creative ideas to engineer out exposures demand a lot of attention and enthusiasm, simply using the information you have to make smarter PPE decisions can have a significant impact on safety.
This will involve:
- Collating and analysing your data for trends using a good safety management system, then embedding this intelligence into your PPE specifications.
- Developing a systematic process for identifying and reporting PPE-related exposures, again embedding these into your SMS.
- Proactively reviewing your PPE procurement list at regular intervals – not just when your supply comes up for tender.
- Engaging with a safety and innovation-led PPE distributor who really understands the value of helping you stay ahead of your workplace exposures.
In many cases, the data is already there – you just need to make sure it is being used appropriately, and hard-wired as consistently into your PPE provision as it is into every other aspect of your SMS approach.
The role of your PPE supplier
The safest companies are in a perpetual state of chronic unease and a continuous improvement loop of feedback and learning. A best-in-class PPE supplier should work tirelessly with you as an engaged, active partner at every stage of your safety improvement process.
At Anchor Safety, we understand the role of data in driving better PPE decision-making and we’re committed to working with you to ensure you are using your data effectively. We’ll interrogate your data for you, then help you to understand what it is really telling you about your current PPE provision.
Find out how we can use our PPE expertise to help you embed a culture of safety, by specifying and sourcing totally fit-for-function PPE that your staff will love to use. Discover Anchor Safety
Customer Care.